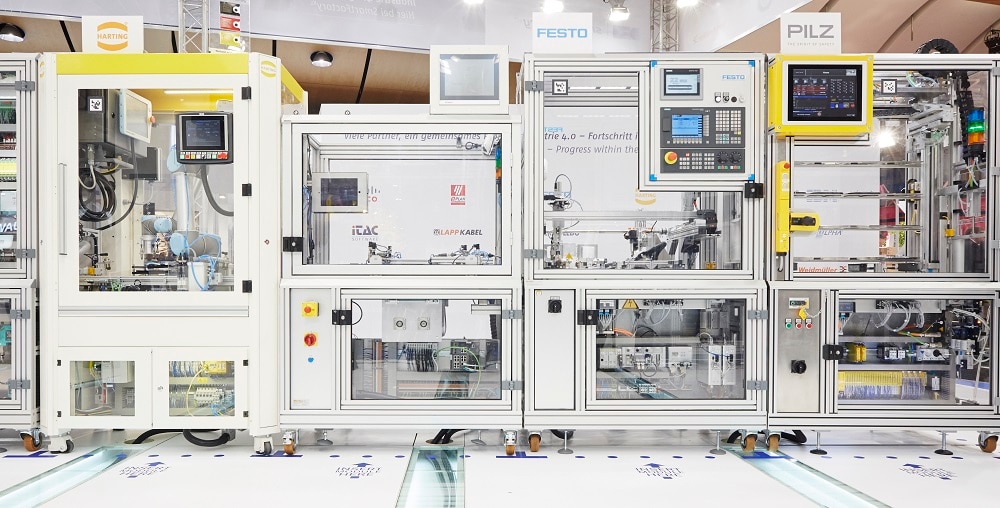
29. September 2021
Smart Factory Summit 2021
How is the automation of the supplier coordinated with the OEM? What can SMEs, especially from the mechanical engineering sector, do to make their manufacturing smart and efficient? What role do equipment suppliers play? How can artificial intelligence help make production smarter? These and other questions will be discussed at the Smart Factory Summit.
Other topics driving digitization and efficiency improvements in the industry include: Lowering manufacturing costs, reducing startup costs, increasing flexibility, utilization and quality, and ultimately, of course, cybersecurity.
Also highlighted are the digital platforms and communication systems needed for a smart manufacturing industry. After all, with the Industrial Internet of Things (IIoT), it is also necessary to network logistics processes and administrative data with production machines. This will enable central real-time monitoring and evaluation of the future smart factory.
Last but not least, users will talk about their experiences and “lessons learned” from their own projects. In addition, the subareas that can be made smart, such as condition/process monitoring & predictive maintenance, will be highlighted and interfaces for the smart factory will be presented.
The summit is aimed at members of management, plant and operations managers, division managers, as well as production managers and executives, particularly from the areas of production IT, production planning, corporate strategy/development, logistics, maintenance, and robotics & automation.
The event is aimed in particular at the automotive industry, OEMs and suppliers, metalworking and processing, mechanical engineering, electronics industry, food industry, packaging and plastics.
The event is supported by our partners in South Africa, Turkey and Morocco. The conference language is German with simultaneous English translation.
Program
10:00 a.m.
Moderation and outlook for the day
Markus Strehlitz, Editor Industrieanzeiger

10:10 a.m.
Smart Factory 4.0 – A win for people and companies
Johann Soder, Chief Operating Officer, SEW-EURODRIVE
New technologies and trends have always changed our world and will continue to do so in the future.
This also applies to Industry 4.0. What is important for this is: Willingness to change and speed in implementation!
In order to tap productivity potentials, the “Working World 4.0″ relies on comprehensive digitization and automation of value creation processes. Flexibility, mutability, networking and self-sufficient modules are the buzzwords for the design and construction of new factories. In future smart factories, for example, mobile assistance systems that navigate flexibly through space cooperate with rigidly arranged conveyor technology. A newly designed smart factory and the achievable results will be presented in the lecture.

10:45 a.m.
Panel discussion: Smart Factory International
- Nissrin Arbesun Perez, Technology Transfer & Innovation Management, Fraunhofer IOSB-INA (Industrial Automation Division)
- Denise Rice, President, Peak Performance, Inc. & Director, Tennessee Manufacturers Association
- Prof, Dr.-Ing. Martin Ruskowski, Chairman of the Board of the Technology Initiative SmartFactory KL e.V.
- Sevda Kayhan Yilmaz, Vice President, Turkish Machinery & CEO, Kayahan Hydraulics
Manufacturing companies are setting about making their plants fit for the future. The goal is the smart factory, in which machines and IT systems are networked with each other. But what are the benefits of the smart factory? Product quality, cost savings, efficiency – where are the potential benefits? And how has the digitization of the factory progressed in an international comparison? Are there differences between individual countries in terms of opportunities and challenges in smart manufacturing?
These questions will be discussed by experts on the “Smart Factory International” panel.


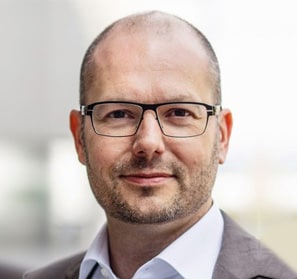

11:15 a.m.
With the Smart Data Fabric to the Smart Factory
Peter Dommermuth, Sales Executive, Intersystems DACH
More and more industrial companies are increasing their investments in the digital transformation of their production, aiming for comprehensive networking of IT and OT systems in the sense of the Smart Factory. And this with growing success, as evidenced by the current study “AI in Manufacturing” by IDC, the most important results of which will be presented in this talk.
The presentation will use real use cases to explain the measurable benefits that companies are already achieving in practice with the use of artificial intelligence and machine learning in the Industrial Internet of Things (IIoT) environment. These include, above all, efforts to increase the overall efficiency of the production plant (Overall Equipment Efficiency – OEE), but also the productive use of Digital Twins and the use of predictive maintenance.
11:35 a.m.
Machine Learning in Industry – Increase Quality & Reduce Waste with Automation
Carsten Riggelsen, Head of Data & ML/AI DACH, AllCloud
The Cloud, IoT, Machine Learning – many new technologies can improve your production and quality assurance. How can you concretely benefit from the new technologies in your business? We will present some exciting news from the fields of Machine Learning and Business Intelligence and report from our practice how German companies concretely benefit from the new technologies in the fields of AI and Data Analytics. We also look forward to a discussion about where the AI journey in Germany will take us.
11:55 a.m.
The manufacture of networked products – a transformative challenge
Francis Cepero, Director Vertical Market Solutions, A1 Digital
In this presentation, Francis Cepero highlights the challenges and opportunities that manufacturing companies face if they want to remain competitive with their products and services in a drastically digitizing market. In doing so, Francis Cepero explains the opportunities that IoT technology brings for new products, processes, services and revenue streams.
12:25 p.m.
Lunch break
01:30 p.m.
Industry 4.0 and Artificial Intelligence: From Hype to Reality
- Dr. Michael Jürgens, Head of AGV Solutions &
- Dr. Christian Liedtke, Head of Strategic Alliances, KUKA Deutschland GmbH
We’re going live to KUKA – to the south of Germany, directly to the company premises in Augsburg. There, Dr. Michael Jürgens and Dr. Christian Liedtke will welcome us in a double interview, moderated by Ulrike Götz, from the in-house Smart Factory. The topic: Industry 4.0 and artificial intelligence: from hype to reality. Where do we stand on these issues? Why are we not yet further ahead? With a view to artificial intelligence, digitalization and data, they will talk specifically about the role of artificial intelligence in a smart factory and where it can provide targeted support, using the KUKA Smart Factory concept as an example. Last but not least, they will touch on the topic of new business models – and look forward to your questions.
02:00 p.m.
Why wait any longer? Eliminate unplanned downtimes with ready-to-install predictive maintenance solutions from igus® – smart plastics
Richard Habering, Head of Business Unit, igus® smart plastics. igus®GmbH
Especially in the current phase, every minute often counts in production plants. Efficient, intelligent maintenance protects against expensive production losses and unplanned downtimes. The service life of igus® e-chains®, cables and bearings can be precisely calculated thanks to years of test experience in the in-house test laboratory – and this is available online and to everyone. Thus there are no surprises in the customer applications. What’s more: with smart plastics, the sensor-equipped components report at an early stage when they are due for replacement. In this article, I would like to show you what distinguishes our predictive maintenance offering and how we have successfully introduced various predictive maintenance projects at our customers – with the intelligent solutions from smart plastics.
02:20 p.m.
Robot simulations and how they facilitate integration into networked manufacturing environments
Benjamin Völzke, Head of Field Application Engineering Western Europe, Universal Robots
The presentation shows how robot simulations can be used to identify accessibility problems and sources of interference at an early stage and to test finished programs. 3D simulations thus reduce unexpected integration costs.
02:40 p.m.
Robotics in Smart Factories
Dr. Michael Klos, General Manager, Business Development , YASKAWA Europe GmbH, Robotics Division
From a robotics perspective, the term “smart factory” is discussed in three contexts:
a) the integration of the robot into the digital process chain (programming, simulation, digital twin).
b) the use of IoT and AI to intelligently monitor and control production.
c) the ease of installation and operation of robots (“smart robotics”, often presented as an entry point into robotics for SMEs).
For this smart technology to be a success, our customers need to see the tangible benefits of this technology for their individual businesses.
Vague terms like “unlocking competitive potential” are not enough – we need a (also critical) discussion about the meaning and added value of this new technology of the future – in comparison or in addition to the proven world of automation as we know it so far.
This presentation deals with practice-relevant implementation proposals from all three listed “smart” robotics areas.
03:00 p.m.
Coffee break
03:15 p.m.
Relevant data at the touch of a button – data intelligence from the field to the cloud
Dieter Horst, Head of Industrial Identification, Siemens AG
Modern production facilities provide countless data and information that often remain unused. The presentation deals with the digital production file and the added value that can be created with it. The digital production file provides information individually for each product about production steps, materials used, test results and much more information. It is based on the principles of the Industrial Internet of Things (IIoT). It offers many advantages and can already be implemented today.
03:35 p.m.
AGVs for the flexible interlinking of production plants in the smart factory
Dr.-Ing. Peter Knappe, Head of Software Development Robot/ PC Technology, IBG Automation GmbH
Products are being adapted more and more individually to the needs of end customers. The resulting diversity of variants requires increasingly flexible adaptive manufacturing processes. Optimal flexibility and utilization of machines and employees can be achieved through free flexible linking of automatic processes, manual work steps and logistics processes by means of driverless transport systems. Additional processes or redundant stations to increase capacity can be easily integrated. This presentation explains the concept using a real application example.
03:55 p.m.
The Intelligent Connector as “Enabler” of the Vision Production Level 4 of the SmartFactory Kaiserslautern
Andreas Huhmann, Physiker, Strategy Consultant HARTING & Vorstandsmitglied Smart Factory KL
To support the vision of “Production Level 4” of the SmartFactory Kaiserslautern (SmartFactoryKL), experts from various manufacturers of connectors and software providers as well as scientific staff from the SmartFactoryKL and the German Research Centre for Artificial Intelligence (DFKI) are jointly developing use cases for an intelligent connector (Smart Electrical Connector, SmEC) with the aim of describing a universal interface for production modules to the supply and communication infrastructure that can also be operated safely by unskilled personnel. These use cases are based on additional functions of the connector that contribute to the realisation of the safety concept of modular production, such as the (self-)locking of the connector under voltage.
04:15 p.m.
Open discussion and summary of the day
Markus Strehlitz, Editor Industrieanzeiger
Veranstalter
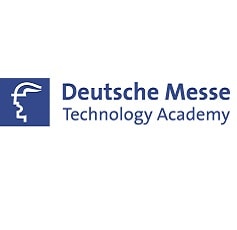
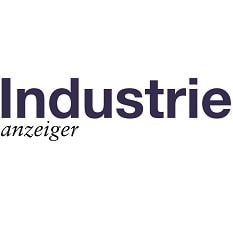